Welcome to our guide on coatings defects! Coatings play a crucial role in protecting surfaces from corrosion, wear, and environmental damage, as well as enhancing their appearance. However, despite their many benefits, coatings are not immune to defects. From blistering and cracking to adhesion failure and orange peel, various issues can arise during the application, curing, or service life of coatings. In this article, we will explore the common types of coatings defects, their causes, and most importantly, how to prevent and address them effectively. Whether you are a professional in the coatings industry or a homeowner looking to maintain the integrity of your surfaces, understanding coatings defects is essential for ensuring long-lasting and high-quality results. Let’s dive in and uncover the world of coatings defects together! Common defects in coatings include
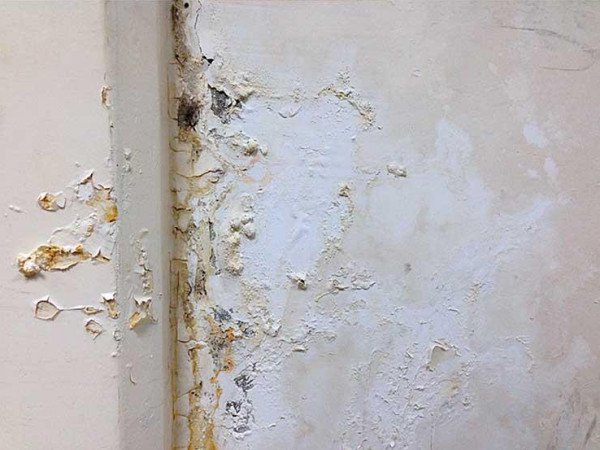
- Blistering: Formation of bubbles under the coating due to trapped moisture or air.
- Cracking: Development of cracks on the coating surface, often due to poor adhesion or excessive thickness.
- Orange Peel: Uneven texture resembling the surface of an orange, caused by improper application or drying conditions.
- Sagging: Downward flow of the coating before it sets, leading to uneven thickness.
- Fish Eyes: Small circular separations in the coating film caused by contamination.
- Peeling: Complete detachment of the coating from the substrate, usually due to improper surface preparation.
- Fading: Loss of color intensity or gloss over time due to exposure to UV radiation or harsh environmental conditions.
- Wrinkling: Formation of creases or wrinkles in the coating, often caused by excessive film build or incompatible layers.
The above defects can affect the appearance, durability, and performance of the coating, so it’s essential to address them properly during the application process.
The application of coatings can sometimes face several challenges, including but not limited to:
- Surface Preparation: Inadequate cleaning or preparation of the surface can lead to poor adhesion of the coating, resulting in premature coating failure.
- Improper Application Technique: Applying the coating incorrectly, such as using the wrong equipment or not following manufacturer guidelines, can result in uneven coverage, drips, or bubbles in the coating.
- Environmental Factors: Factors such as high humidity, extreme temperatures or dust in the air can affect the application process and the curing of the coating, leading to defects.
- Compatibility Issues: Applying a coating that is not compatible with the substrate or with other coatings already present can lead to chemical reactions, poor adhesion, or other issues.
- Thinning and Mixing: Incorrectly thinning the coating or improper mixing can affect the performance and appearance of the coating, and may lead to inconsistencies in the finish.
- Health and Safety Concerns: Many coatings contain harmful chemicals that can pose health risks if not handled properly. Ensuring proper ventilation, protective gear, and safe disposal of materials are crucial.
- Quality Control: Failing to check for defects, verify thickness, or conduct proper testing can result in subpar coatings that may not provide the desired protection or aesthetics Addressing these issues through proper training, adherence to guidelines, and quality control measures can help improve the application of coatings and ensure successful. outcomes