Cold Galvanizing Coating:
Cold Galvanizing Coating:
Corrosion is a common problem faced by metal materials, leading to degradation and reduced lifespan. To combat this issue, cold galvanizing coatings offer an effective solution. It involves applying a zinc-rich coating onto the metal surface, creating a barrier that protects against corrosion and rust.
The process of cold galvanizing is simple and can be performed even without specialized equipment. A zinc-rich paint or primer is applied by spraying The coating onto the cleaned and prepared metal surface. The paint contains a high percentage of zinc powder, which acts as a sacrificial anode when exposed to moisture or other corrosive elements. In the presence of corrosion-inducing agents, the zinc sacrificially corrodes instead of the metal, thereby protecting the underlying surface.
Cold galvanizing Coatings provide several advantages over hot-dip galvanizing, another popular method of protecting metal surfaces. Hot-dip galvanizing involves immersing the metal in a bath of molten zinc, which can be cumbersome and impractical for certain applications. Cold galvanizing, on the other hand, allows for easy touch-ups and repairs, making it more versatile.

Why Choose Cold Galvanizing Coating?
- Convenience: Cold galvanizing coating can be done in the fabricating shop or on site.
- Repair: It’s often used to repair weld burns or other damage to newly galvanized steel.
- Primary protection: It can even be specified as the primary galvanizing system.
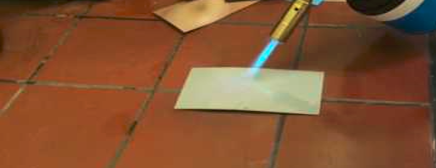
Another advantage of cold galvanizing is its versatility in terms of application methods. It can be applied using brush, roller, or spray, depending on the size and intricacy of the metal surface. This flexibility makes it feasible for both small-scale touch-ups and large-scale coating projects.
Tips for Cold Galvanizing Coating Success:
Material selection:
- Choose Steel with carbon contents below 0.25% to reduce susceptibility to embrittlement.
- OPT for aluminum-killed steels, which show less strain-age embrittlement.

Cold-Working Considerations:
- Cold-worked steel less than 1/8” (3mm) thick are unlikely to experience embrittlement.
- Maintain a bending radius of at least three times the section thickness.
- For carbon content between 0.1% and 0.25%, stress-relieve the material if bending is less than 3 times.
- Drill holes instead of punching them in material thicker than ¾” (19mm).
- Flame-cutting or sawing is preferred, especially for heavy sections.
- In critical applications, hot-work the steel above 1200°F (650°C).

Strees-Relieving:
- Where cold-working cannot be avoided, stress-relieve the part at 1100°F (593°C) for one hour per inch (2.5cm) of material thickness.
Certainly! Let’s succinctly highlight United Colorama Group’s Galvazinc 9600
Galvazinc 9600:
- Zinc Concentration: 96% pure zinc metal in the dry film.
- Description: Galvazinc 9600 is our premium cold galvanizing solution. With its high zinc content, it provides exceptional corrosion resistance and durability.
Technical & Physical Information (@ 25°C)
Ingredients : Pure zinc metal (6 microns) + Volatile Hydrocarbons + Organic Binder
Finish : Homogeneous Grey Matt Film
Total Zinc Content in DF :96%
Density :3.5 Kg/L ± 2%
Solid Contents :51% (By Volume) and 88% ( By Weight)
Flash Point :67°C
Dry Film Thickness :50-125 microns
Th. Spreading Rate :10.2 m²/L @ 50 microns DFT
Touch Dry :30 min.
Recoat Interval :4 hour
Complete Cure :24-36 hours
VOC :33 g/L
Temperature Range From :(- 50°C) To (+ 180°C)
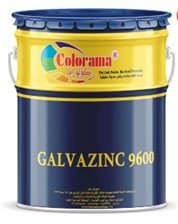
5.Fields of Applications:
GALVAZINC is an ideal easy to apply cold galvanizing coating material for all small and big steel objects and can be used for:
– Pipelines (Surface or immersed).
-Steel structures.
– Fuel and chemicals holding tanks.
– Chassis and bodies for cars, planes, trains and all transport Vehicles.
– Steel bridges.
– Barrages , dams and locks gates.
– Corrugated , icon sheets and sandwich panels.
– All small steel works.
– Ships, yachts, cranes and all marine structures.
– Nuclear energy plants.
– Electrical power plants.
– Store shelves and handling tools.
– Metal and electronic gates and escalators.
– Mineral belt conveyors.
– Grain storage silos.
– Rebar and construction equipment.
Ready to transform your results?
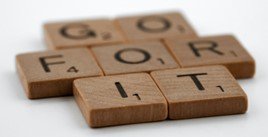